3 Effective Ways Manufacturing Firms Can Improve Operational Efficiency
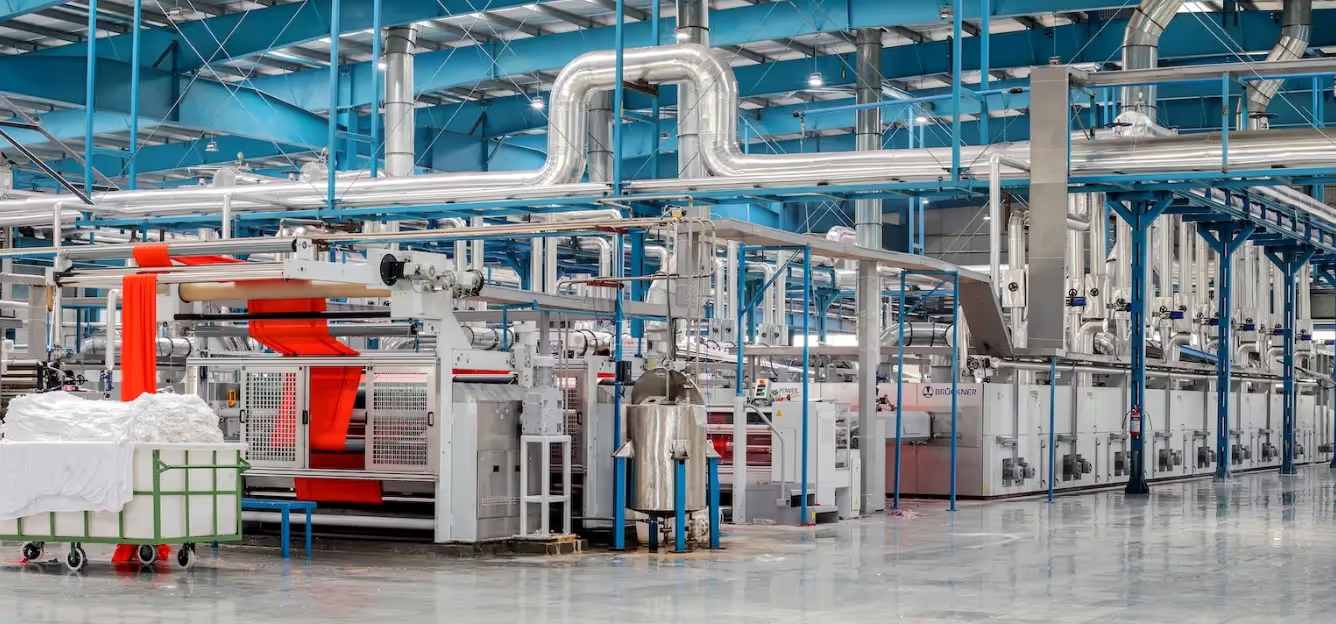
In a general business context, a company’s operational efficiency determines whether it is running on a continuous cycle of improvement. It is only then that the ratio between the firm’s output and input required is good.
This means a manufacturing organization’s operational efficiency is said to be excellent when it can produce high-quality products, keep its customers satisfied, and reduce wastage of time and resources simultaneously.
However, the question of the hour is how manufacturing companies’ operational efficiency can increase. This article talks about three effective ways to do so.
Increased Focus on Automation
Did you know that in 2021, at least 3.5 million robots were employed across worldwide manufacturing firms? These robots carried out 50% of the manufacturing work. The Harvard Business Review even states that a new generation of robots can support small manufacturers.
The need for automation is so fundamental in the manufacturing sector that it is not limited to large enterprises. It is a much-needed boon in a talent crunch where companies are facing recruitment challenges.
Keeping the talent hunt aside, the manufacturing macro-environment is quite demanding. It involves relentless cycles of tight deadlines, restricted profit margins, ever-changing consumer preferences, and supply chain issues.
An increased focus on automation is the only way to not only maintain operational efficiency but also survive in the market. A shutdown or slight delay in the production line can lead to adverse consequences.
Real-time monitoring enables manufacturers to keep track of the supply chain and identify issues early on. These can be addressed way before they lead to costly downtimes or compromised product quality.
Furthermore, automation can help manufacturing firms improve metrics like safety and labor costs. This will happen as employees need not perform dangerous tasks. Naturally, operational efficiency will improve.
Hiring the Right People (+ Employee Training)
In a lot of cases, manufacturing firms suffer the consequences of an incompetent team, especially on the operations front. This turns the table upside down on the input-output ratio. Having the right people on the team can make a huge difference in improving operational efficiency.
For instance – the operations manager must have a Master's degree in operations management with experience in project and technology management. This will ensure they have a clear idea of how to integrate operational activities of different functional areas.
According to Kettering University, the combination of theory with practice trains such individuals to make a positive impact right away. After all, those holding influential leadership positions must know how to link people, workflow, and performance.
The same goes for other members of the team. It is important to verify the candidate’s credentials and work experience before hiring. Also, the job description must be thorough and clear, stating all requirements of the respective role.
Besides a well-planned recruitment process, manufacturing firms need a solid training program in place. The industry is constantly evolving, especially its technological aspect. When employees are up-to-date, they are less prone to making mistakes that may affect productivity and efficiency.
Having Strict Quality Control Measures
Another way to improve operational efficiency and ensure consistent product quality is to introduce strict quality control measures. What a manufacturing firm (both small and large) needs is to implement a Manufacturing Execution System (MES).
Without it, operators may fail to realize a defect early enough to take corrective steps. This will lead to bad-quality products, customer dissatisfaction, delays in time-to-market, and wastage of time and resources. It also marks the brand in the customers’ eyes as one that does not focus on continuous improvement.
Every manufacturing firm must define its suitable quality example and then conform its products to those specifications. This includes the three components of design, quality control, and quality management.
In other words, the core product’s design, functionality, and material choice must be solid. Then, defects from the manufacturing process should be eliminated to match the original design. Finally, all tasks involved in product manufacturing must aim to achieve the desired level of excellence.
When potential risks and hazards are detected under each step, it becomes easier to tackle them. This streamlines the operations and leads to better productivity.
As we close, mention must be made of how quickly modern technology is changing the manufacturing company’s operations game. The worldwide manufacturing operations management software market is growing at a CAGR of 12.9% till 2030.
The expanding market is attributed to an increased need for real-time monitoring and tracking. Industry 4.0, in the form of Artificial Intelligence and Machine Learning, is boosting exponential growth. As the years go by, we will see organizational efficiency largely being handled by technology.